Discover the craftsmanship and traceability behind linen
- Share
- Issue Time
- Nov 22,2024
Summary
Exploring the production process of linen from cultivation to weaving, and demonstrating its eco-friendly characteristics and quality touch, Linenwind combines linen with cashmere and silk through handcraft and modern technology to create innovative fabrics that are both comfortable and sustainable.
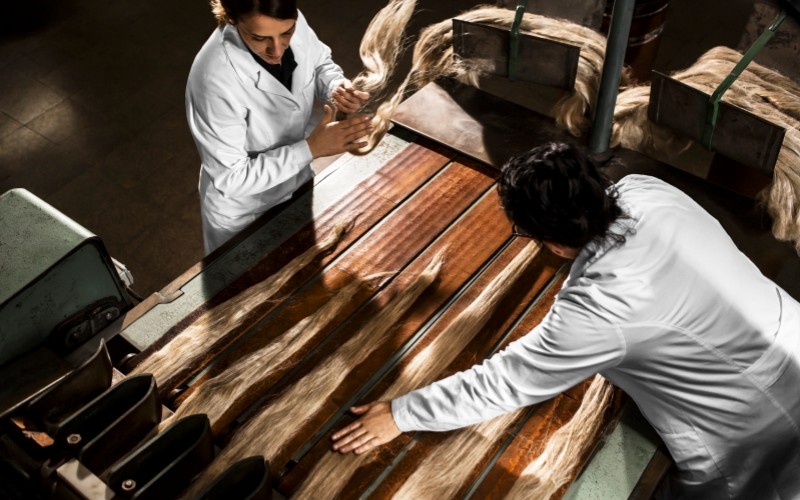
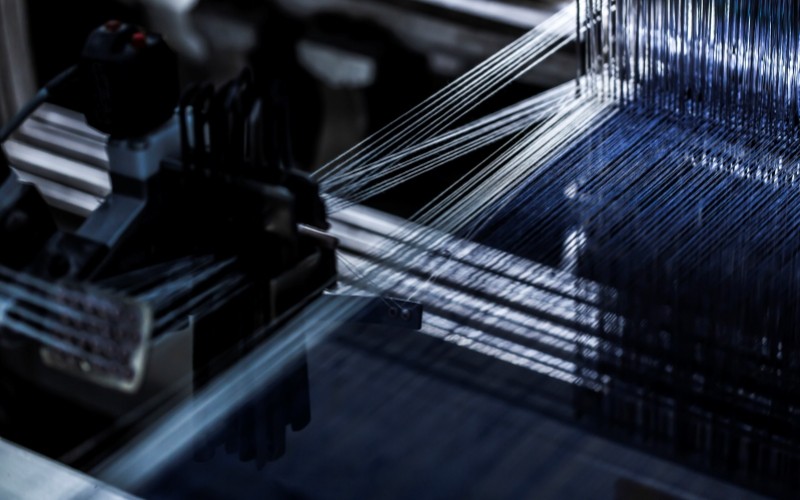
It is a collection of casual elegance, refreshing, soft texture as one of the precious fiber. Luxurious and comfortable to the touch, practical and versatile.
Always striving for excellence, we focus on transforming high-quality yarns into fabrics that combine craftsmanship with lasting elegance and unique touch, and linen is a model among them. Our factory has been a leading player in the production of flax for the past 150 years and has been an integral part since 2013. Thanks to their deep knowledge, the brand artisans create new textures by blending linen yarns with precious cashmere, silk and wool to transform fabric structure, appearance and texture. The linen and cashmere blend combines the breathability and lightness of linen with the warmth and soft touch of cashmere, so it can be worn all year round.
Flax is inherently more sustainable than other crops, requires less water and is more resistant to pests. Flax itself can also be antibacterial, anti-pilling, with excellent air permeability and effective moisture absorption. The brand and the flax growers are committed to the highest quality, transparency and local production.
From the naturally hard roots of the flax crop, to the fine flax fibers, to the comfortable garments that add the brand's signature elements, it is a long and meticulous process. The first step is the planting and harvesting of flax. Flax is produced in the natural humid climate regions of China, and these two regions are known for producing high-quality flax. Selecting fiber is a professional technology, which needs to be integrated with viewing and touching.
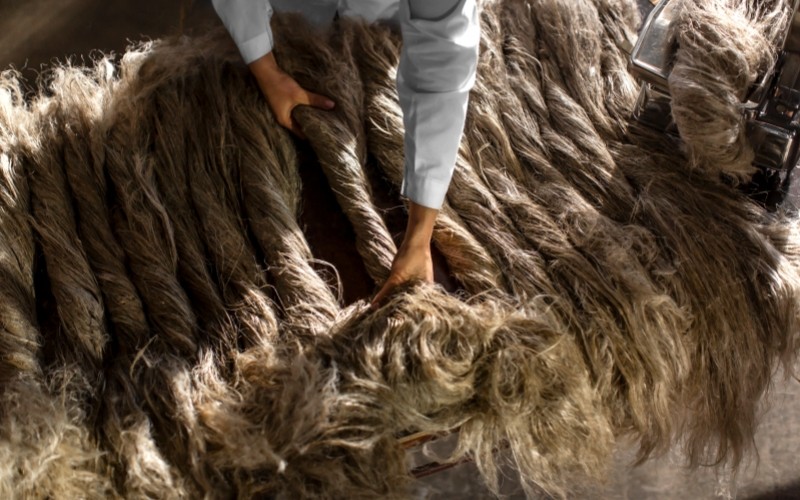
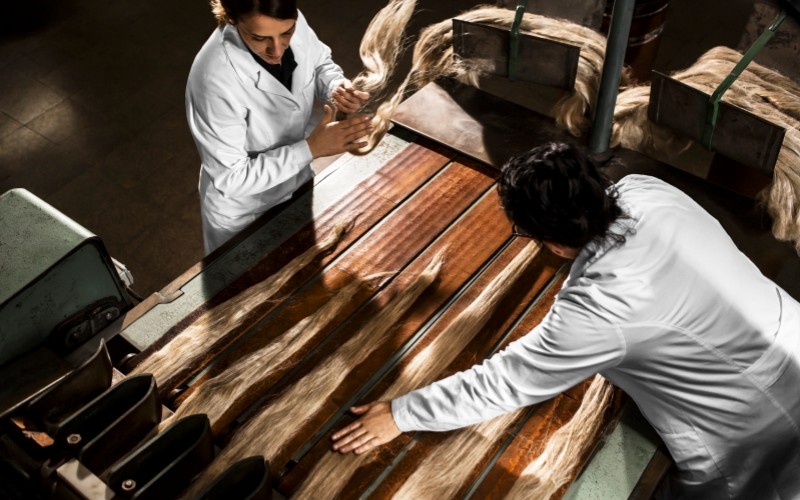
After harvest, the dried flax is treated with maceration, usually by soaking it in water or rain to release the fibers from the stems through monitored natural degradation. The ideal fiber is separated from the plant xylocore by beating. Traditionally, flax is separated by hand by artisans to ensure it is intact and free of impurities. This handmade method not only ensures better linen quality, but also pays tribute to ancient traditional textile techniques.
The next stage is the comb. At this stage, the extracted long and short fibers are separated and carefully arranged in preparation for spinning. These fibers are then arranged into parallel bundles of flax, laying the foundation for a strong and flexible yarn. After the hemp strips are formed, spinning can begin.
Professional craftsmen carefully inspect and adjust each piece of hemp to ensure that each piece of silk is uniform. Skilled spinners carry out coaxial fiber spinning, and every twist of the spindle bears witness to the birth of high-quality linen yarn. Use the highest quality linen of its kind. This means that one kilogram of linen thread can be stretched up to 110 kilometers. The fabric is produced in the brand's factory through a process of warp carding and weaving, which requires meticulous precision. During the finishing stage, flax is soaked in aloe vera juice to enhance its antibacterial and hygroscopy properties, while giving it a soft texture and signature style. Extensive research, the search for quality raw materials, the use of fine yarns, and innovative technologies to create new blends and finishes make linen truly unique.
